Lean Six Sigma: Bridging the Gap Between Productivity and Safety Compliance
A synergistic relationship where safety and efficiency reinforce each other
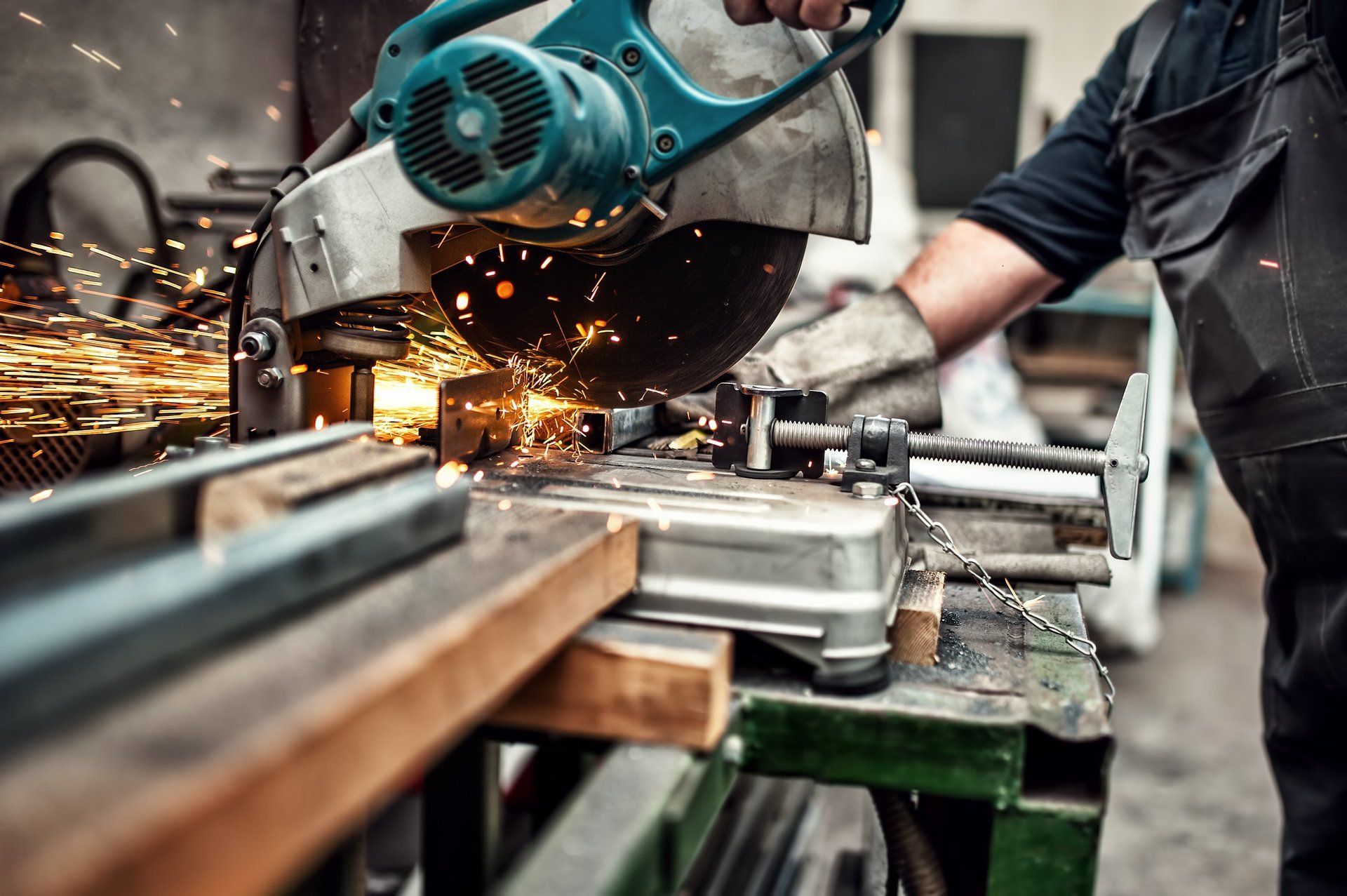
In the manufacturing industry, much like most industries, the pursuit of increased productivity and strict adherence to safety compliance often seem to be at odds. The pressure to maximise output can inadvertently lead to corners being cut in safety protocols, while stringent safety measures can sometimes be perceived as hindering productivity. However, Lean Six Sigma, a methodology focused on improving efficiency and eliminating waste, offers a compelling solution to harmonise these two critical aspects of manufacturing.
Harmonising Safety and Efficiency
The core philosophy of Lean Six Sigma revolves around streamlining processes, reducing waste, and enhancing quality. When applied thoughtfully, it can significantly improve safety compliance without compromising productivity. In fact, it can lead to a synergistic relationship where safety and efficiency reinforce each other.
One key concept in Lean Six Sigma is the identification and elimination of non-value-adding activities. In the context of safety, this can mean simplifying safety procedures without reducing their effectiveness, thereby making it easier for employees to comply and reducing the time taken in following these procedures.
Techniques for Balancing Safety Compliance and Productivity
Lean Six Sigma employs several techniques that are particularly effective in achieving this balance:
- Process Mapping and Analysis: By mapping out processes, manufacturers can identify steps that contribute to safety risks or non-compliance. These steps can then be redesigned or improved to enhance safety while also making the process more efficient.
- Root Cause Analysis: This technique involves identifying the underlying causes of safety incidents or compliance issues. Addressing these root causes often leads to process improvements that enhance both safety and productivity.
- Standardisation of Processes: Standardising work processes not only ensures consistency in quality but also in safety practices. This standardisation reduces the variability that can often lead to accidents or non-compliance. It also makes policing adherence to processes and safety protocols much simpler and more effective.
- Continuous Improvement: Lean Six Sigma encourages a culture of continuous improvement, where processes are regularly reviewed and improved. Something the HSE are keen to see in all industries, not just manufacturing. This ongoing process keeps safety and productivity at the forefront, ensuring that one does not improve at the expense of the other.
Case Studies Illustrating Successful Balance
Several manufacturing companies have successfully used Lean Six Sigma to balance productivity and safety compliance. For instance, a chemical manufacturing plant utilised Lean Six Sigma methodologies to redesign its material handling process. The new process not only reduced the time taken to handle materials but also significantly lowered the risk of hazardous spills, thereby, enhancing safety compliance.
In another example, an automotive parts manufacturer applied Lean Six Sigma to its assembly line. By analysing, simplifying, and improving their workflow, they reduced the amount of manual handling required by individuals and therefore reduced the physical strain on workers, decreasing the risk of injuries. The by-product of this process improvement was that it increased the number of units produced by a staggering 12%.
Challenges and Considerations
While Lean Six Sigma provides a framework for balancing safety and productivity, its implementation is not without challenges. The most significant of these is resistance to change. Employees and management alike may be sceptical about new processes, especially if they perceive them as adding more complexity to their work.
To overcome this, it's crucial for leadership to be involved and committed to the Lean Six Sigma initiatives. They should clearly communicate the benefits of these changes, not just for the company, but for the employees' safety and ease of work. Additionally, involving employees in the process improvement exercises can help in gaining their buy-in and making the transition smoother.
Conclusion
In conclusion, Lean Six Sigma offers a robust approach to harmonising safety compliance and productivity in the manufacturing industry. By focusing on process improvement, waste reduction, and continuous improvement, it provides a pathway for manufacturers to enhance their safety standards without sacrificing efficiency. As more companies adopt this methodology, we can expect to see a shift in the manufacturing landscape, where safety and productivity are no longer at odds, but rather, work in tandem to create a more efficient, safer, and more profitable manufacturing environment.
Transform Your Manufacturing Process with Consulo
As you've seen, the balance between maintaining rigorous safety standards and achieving optimal productivity is delicate but crucial. At Consulo, we specialise in turning this challenge into your competitive advantage. Our expertise in Lean Six Sigma methodologies uniquely positions us to help your manufacturing company not only identify areas where safety can be significantly improved but also enhance overall efficiency and profitability.
Imagine a workspace where safety and productivity coexist in harmony, where compliance is not a hurdle but a stepping stone to greater success. That's the environment we strive to create for you. Our team of experts will work closely with you to analyse your processes, identify key areas for improvement, and implement targeted strategies that bring about tangible, positive changes.
Don't let the complexity of trying to improve both compliance and efficiency slow you down. With Consulo, embark on a journey towards a safer, more efficient, and profitable manufacturing process.
Contact us today to learn more about how we can make this vision a reality for your business. Together, let's redefine what's possible in manufacturing!
Take the First Step Towards Excellence – Reach out to Consulo Now.
